Handloaders are generally constrained to less resource-intensive methods than commercial shops for confirming that pressures are within reasonable levels. We often see these techniques discussed:
- primer flattening and or cratering,
- loose primers,
- gas leakage around primer pocket,
- blown primers,
- difficult extraction (hard to detect with semi-automatics),
- case head expansion,
- strain gage.
All of the methods available to the handloader experience some degree of controversy. See, for example:
and
The truth about “pressure signs”
The concerns expressed are valid. Of these, only the strain gauge method comes close to mapping into commercial load databases but the cost of the equipment and related hardware is normally several hundred dollars.
As a result, a large number of serious handloaders continue to use the older methods because they represent the only tools available for detecting an approach to significantly high pressures. The case head expansion technique can be useful for the careful and knowledgeable hand loader. Let’s take a closer look.
The first step is to acknowledge the rebuttal of Ken Water’s “Pressure Ring” method by Bramwell (“PRE, CHE, RIP” ). Ken Waters method measures the change in diameter just above the web of the base where the brass is a little thicker than the rest of the case wall. This is not a location that produces behavior that is analogous to the copper crusher cylinder. Bramwell’s rebuttal, while accurately critical of the pressure ring method, does not address the case head expansion technique.
Furthermore, gas-operated firearms like those in the AR family frequently allow the case to start extracting while some pressure remains in the chamber. The resulting rings look like Water’s pressure rings but are meaningless in the context of pressure measurement. We are still able to use case head expansion, however, because that part of the case is not supported by the chamber, so the timing of the action opening cycle is less critical.
Let’s turn to a discussion of about how to do the measurements in a way that parallels the commercial laboratory crusher cylinder method. Unlike the crusher cylinder, this method works in your chamber and does not result in a pressure estimate. The method instead generates a picture of the behavior of your brass in your chamber. You will also invest 20 or more rounds of trigger time plus a little chronograph work provided you have one.
Reader beware: Validating this method is more in your hands than one might first think. The method asks that you first calibrate against factory ammunition or known handloads with the same lot of unfired brass you plan to use for your ladder test1 or round robin series. Second, the method also asks you to draw up a scatter plot showing the head expansion for each of the shots you made in the ladder test. You will do something similar with the impacts on the target so it is a small extension of what you already do. You will be able to get a good idea of whether the data are meaningful by a quick perusal of the plot. The points do not need to appear to be in a neat line, but you do want to see a discernible trend.
If you don’t get what appears to be a recognizable trend, two things are possible. First, the measurements may have been taken too high on the case and you were actually measuring the pressure ring expansions. The second possibility is that you were measuring the rim diameter. It is also possible that the method doesn’t work for you.
THE METHOD Step 1: Establish a Baseline for Your Rifle and Brass –
Build the baselines2 using a known load in unfired brass from the same lot as what you plan to use for developing your loads. You can also use factory loads in the same brand. Plan to shoot at least five of these loads, preferably over a chronograph, to establish your baseline expansion.
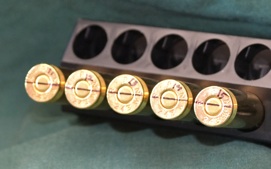
Scribe and number the unfired cartridges.
-
Use a fine line permanent marker to scribe a reference line across the bases
-
Number the cases for reference.
-
Measure the diameter in the direction defined by the line and record by case number.
-
Shoot the factory ammo or trusted handloads and repeat the measurement & recording.
-
Subtract the unfired diameter from the diameter of the now once fired case. Use the case number to make sure the measurements are consistent.
-
Note the scatter and average of your case head expansions.
You can now use the extreme spread and average of your baseline head expansion tests as a reference for your load development.
THE METHOD Step 2: Make a scatter plot from your ladder or OCW test results –
-
Use a fine line permanent marker to scribe a reference line across the bases of the loads you plan to use. (ALWAYS USE UNFIRED BRASS — fired brass gets work-hardened, and generates reduced expansion for the same pressure. This does not err on the side of safety.)
-
Number the cases for reference.
-
Measure the diameter in the direction defined by the line and record by case number.
-
Shoot the ladder or OCW test, recording the normal information.
-
Measure the new case head diameters using the same technique as above.
-
Subtract the unfired diameter from the diameter of the now once fired case. Use the case number to make sure the measurements are consistent.
-
Create a scatter plot of the differences in case head diameter versus charge weight.
-
Compare the plot with the average and scatter of your reference loads (factory or known safe reloads).
This approach will not yield specific pressure data, but you can get an idea of trends and generic relative pressures. Most importantly, you develop a better understanding of how your brass behaves in your chamber.
Many users of the scatter test compare plots of velocity vs charge weight in addition to plots of impact height versus charge weight. Adding a plot of case head expansion versus charge weight may help add more insight into your search for one or more sweet spots. Similarly, the careful handloader will continue looking for all of the customary signs of serious pressure as a continuing double check.
Leave a Reply
You must be logged in to post a comment.